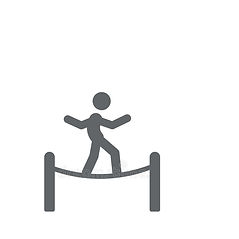
Beeing a leader or a coworker is a constant cooperation / balancing act with others
In my experience one of the more important areas to address is the balance between feeling and logic,
in my vocabulary Heart and Mind

Heart and Mind Management provides Assessment, Coaching, Training, Workshops supporting in management and organisation effectiveness
I have recorded spoken presentations on the following subjects and launched them, and also updated the homepage

Maneuverability
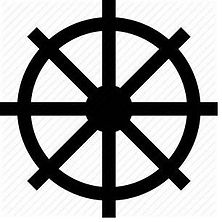
Your organisation needs to:
-
Be motivated
-
Work together as a group
-
Come with ideas for change and development
-
Change and develop
-
Feel supported, seen and listened to
-
Aim for the same goals

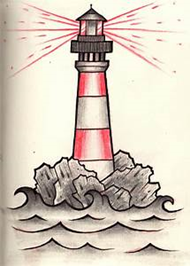
A way to work to reach the targets
Develop a Strategic Focus (the aim for the organisation)
To develop the focus you go through a Strategic reasoning, a way to logically frame your targets in relationship with the overall targets.
To create a lighthouse for the organisation to work towards and the reasoning why we need to go there
Change is needed to get there

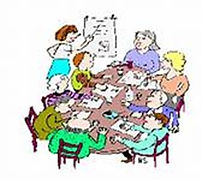
Change groups
-
Divide the working force into change groups (around 8 persons in the group depending on the nature of the Strategic Focus, they can consist of persons within a working team - or may have to be cross-functional)
-
Start up the Change group
-
The Change group works and steers itself
-
The group works 8 to 9 weeks to create a suggestion and work together to create the change (in this phase the group needs to contact experts and others involved in the concerned process or organisations)
-
The Change work is presented to the other teams, to the Manager and the Manager’s Manager

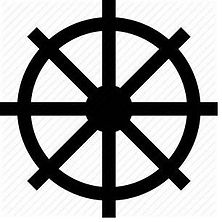
This way of working creates a climate where
-
Change is a natural part of everyday life
-
You show the coworkers that change is important and worth the time to work with (the Manager and the Manager’s Manager come to the meeting)
-
An environment where everyone is listened to, respected supported and seen
-
You promote teamwork

Homepage:https//www.heartandmindmanagement.com
Maneuverability | Heartandmindmanagement | Västra Götalands Län

Innovation
Is a new idea, for instance a product, solution, business idea, service, chemical formula, material, mathematical methododology, technical solution that shows itself promising to, or does, work.
It fullfills a need or a demand.
It is not previously known, publicly.
A later definition includes the above - but not until it has reached the market.

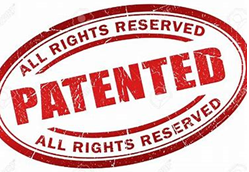
Patent is an exclusive right to use an innovation : No one may produce, sell or import it without the Patent owner’s permission.

Patents
could be used for different purposes


-
Protect the solution that you have invented
-
You patent the solution you intend to use
-
Protect other solutions that could limit your original solution
-
Patents on different solutions around the solution that you have developed


The stronger protection you want from a Patent,
-
the more expensive it is (more nations)
-
the broader scope you need
While developing an Innovation it is important to investigate the Patents that this Innovation could be influenced by
To infringe someone’s Patent might be very expensive
When performing patent work, do use experts !
Problem Solving Methodologies

When we see a problem we tend to look under the lamp and to jump into an early conclusion of how to solve it
It feels good to do something about it quickly
but give it a little time and thinking to really solve the problem with a suitable solution to ensure that the problem will not reoccur
Core Principles
Concentrate on solving reoccurring root causes rather than solving just symptoms
-
Do not ignore the importance of treating symptoms for short term relief
-
There can be, and are, often more than one root cause
-
Analyse using the 5 W and H method (Ask Who?, What?, Where?, When?, Why? And How? Did the problem show up?)
-
Be systematic and look for evidence to back up the found root cause
-
Try to find a way to solve the root cause to prevent it from appearing again
-
When performing a Root cause analysis it is important to take a comprehensive and holistic approach and to use all the knowledge available in the entire organisation (Cross functional)


Root Cause
To investigate what the real problem use:
5 W + H
-
Who does it concern?
-
What happened?
-
When did it happen?
-
Where did it happen?
-
Why did it happen?
-
How did it happen?


Change analysis
Analyse the changes that has led up to the problem
-
Looking on a longer period of time leading up to the problem
This is effective when there are a number of root causes

Fish bone analysis
A way to analyse root causes is the Fish bone analysis (Ishikewa diagram analysis), where you start with the problem and work your way back through different possible causes of the problem
Categories to consider in the analysis
-
Machine (equipment, technology)
-
Method (process)
-
Man/Mind(physical or knowledge)
-
Measurement (inspections)
-
Management /money power (leadership)
-
Maintenance
-
Product/Service
-
Price
-
Promotion(Marketing)
-
Process (System)
-
People (Personal)
-
Physical evidence
-
Performance
-
Surroundings (Environment)
-
Suppliers
-
Skills


Ensured Start Of Production
Is a concurrent and cross-functional approach to secure a smooth and quality-ensured industrialisation ramp up. An important milestone in a project.
Depending on what you produce (product or services), Start of production is done in different ways
The common target is to minimise the problems during Start of production and give time to correct ocurring problems

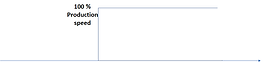
The Jump Start
The Production Process might demand it
There is no room for errors in this scenario
– to make sure that they don’t occure, design for assembly meetings and simulations need to be performed early in the project

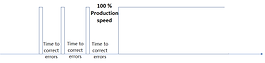
The Batch Start
Batchwise production until reaching 100% production speed
This way of acting gives time for correction between the batches

The Ramp up Start
Slowly ramping up the production speed to see problems earlier and have the time to work around them, but not forgetting to solve the root problem this way gives the coworkers that are to produce, time and possibility to learn how.


The Ramp up and Batch trials Start
This way intends to use the advantage of both ways (Batch and Ramp up) so you run batches full speed during the ramp up
Problems are often speed related and are caught in the batches while the ramp is there to teach the production line how to produce

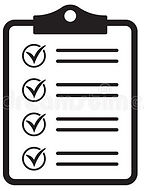
Companies tend to have checklists that are used during Start of Production – making sure that all problems are found
All problems that occur late in the process are expensive to correct
Design for Assembly needs to be performed from early in the project, no matter what way you chose to start production,
To change a design before prototypes/machine parts/modules are bought is a lot cheaper than when the production has started

To get involvement from everyone early in the project is easy to say but not so easily achieved
-
Within an organisation we tend to work with the same time perspective, which is not true between organisations.
-
E.g. Product Development typically work with new Products that take years to develop.
-
In Production you work with things that need to be mounted now.
Homepage:https//www.heartandmindmanagement.com
https://www.heartandmindmanagement.com/kopia-p%C3%A5-assured-start-of-production

Planned are 4 workshops during August2023
-
No cost for participating
-
No limit in numbers attending the meetings

Organisational Design
11/9 2023
10.00-10,30
17.00-17.30
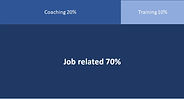
Competence management
18/9 2023
10.00-10,30
17.00-17.30